Clevere Technologie im Namen der Sicherheit
Posted by: Unknown author
Prüfstrassen zur Brems-, Fahrwerk- und Spur-Diagnose sind heute elektronisch gesteuert und bieten vielfältige Auswertungs- und Dokumentationsfunktionen. Aber wie funktionieren eigentlich die einzelnen Komponenten? Ein kleines Erklärstück für Branchenprofis.
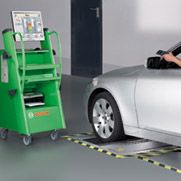
Die mikroprozessorgesteuerten Rollenbremsprüfstände von Bosch ermöglichen einen vollautomatischen Prüfablauf in weniger als drei Minuten und lassen sich zur kompletten Prüfstrasse ausbauen.
Moderne Prüfstrassen sind modular aufgebaut, als offene Systeme. So lassen sich neue Systemkomponenten ohne viel Aufwand installieren. Häufig sind Steuerungs- und Leistungselektronik direkt in die einzelnen Komponenten (Bremsprüfstand, Fahrwerktester, Spurplatte) integriert. Die Steuerung/Bedienung sowie die Auswertung und Anzeige der Messergebnisse wird zentral vorgenommen, beispielsweise über einen PC.
Bremsprüfstand
Rollenbremsprüfstände verfügen über speziell beschichtete Laufrollen, welche einen hohen Reibfaktor aufweisen und gleichzeitig abriebfest und reifenschonend sind. Die Rollenpaare jeder Seite werden von jeweils einem Elektromotor angetrieben, und ein Kettenantrieb verbindet die beiden Prüfrollen kraftschlüssig. Die beim Bremsen auftretenden Reaktionskräfte werden mit Sensoren aufgezeichnet, und die integrierte Mikroprozessorsteuerung wertet die Messergebnisse aus.
Zwischen den Laufrollen ist jeweils eine Tastrolle platziert, welche den Radlauf kontrolliert (Schlupfprüfung). Die Tastrollen sind zudem für die Schalt- und Sicherheitsfunktion des Prüfstandes verantwortlich.
Fahrwerktester
Nach wie vor stellt das Prüfen von Stossdämpfern (Schwingungsdämpfern) im ausgebauten Zustand die verlässlichste Methode dar, um eine Aussage über den Zustand eines Dämpfers zu machen. Denn nur so kann ein Dämpfer ohne Einfluss der Kinematik und weiterer Komponenten beurteilt werden. Fahrwerktester dagegen beurteilen die Stossdämpfer im Gesamtsystem, und die Messgrössen können von weiteren Parametern beeinflusst werden, beispielsweise dem Reifendruck.
Die Tester versetzen das Fahrzeug bzw. die Stossdämpfer in Schwingungen, welche nach verschiedenen Methoden betrachtet und ausgewertet werden. Dabei kommt, je nach Hersteller, entweder das EUSAMA- oder das Boge-Prinzip zur Anwendung. Der Hauptunterschied zwischen den Prinzipien liegt darin, dass zum einen Kräfte (EUSAMA) und zum anderen Wege (Boge) gemessen und ausgewertet werden.
Boge-Prinzip
Bei der Resonanzmethode oder dem sogenannten Boge-Prinzip wird die Radauflage des Testers in Schwingungen versetzt. Diese Oszillation wird durch eine Exzenterwelle erzeugt, die von einem Elektromotor angetrieben wird. Beim Erreichen der Maximalfrequenz wird der Elektromotor von den Prüfplatten abgekoppelt, und die Prüfplatten, welche über Schraubenfedern schwingend gelagert sind, können freie Schwingungen ausführen. Mit einem Sensor wird nun der Weg der Platten gemessen. Eine gute Dämpferwirkung ist dann vorhanden, wenn der Dämpferhub in diesem Bereich einen festgelegten Wert nicht überschreitet.
Die Messwerte werden mit Grenzwerten verglichen, die im Vorfeld vom Testgerätehersteller für jedes Fahrzeug individuell ermittelt werden müssen.
EUSAMA-Prinzip
Beim EUSAMA-Prinzip werden im Gegensatz zum Boge-Prinzip keine Wege, sondern Kräfte gemessen, aus denen Rückschlüsse auf die Dämpfung gezogen werden. Der EUSAMA-Wert (relative Bodenhaftung) bildet sich aus dem Quotienten der minimalen dynamischen und der statischen Radlast.
EUSAMA-Fahrwerktester bestehen aus zwei Schwingplatten, die nacheinander einer sinusförmigen Bewegung mit variabler Frequenz und mit konstanter Hubhöhe ausgesetzt sind. Ein Elektromotor treibt einen Exzenterantrieb an und ermöglicht die Hubbewegung der Platten. Die Schwingplatten sind zudem mit Sensorik-Komponenten ausgestattet, die es erlauben, die Gewichtskraft zu messen. Dabei entspricht die statische Radlast der Gewichtskraft bei «stehendem» Rad. Die minimale dynamische Radlast wiederum ist die gemessene Gewichtskraft im «oberen Totpunkt» des Rades.
Der EUSAMA-Wert liegt immer zwischen 0 und 100 Prozent, wobei 0 Prozent ein für kurze Zeit ohne Fahrbahnkontakt «in der Luft schwebendes» Rad bedeuten würde, über welches keine Kräfte, wie zum Beispiel Lenkkräfte, mehr übertragen werden könnten. Bei einem Wert von 100 Prozent (dynamische Radlast = statische Radlast) liessen sich zwar permanent die gleichen Kräfte übertragen, im Gegenzug wäre jedoch der Fahrkomfort massiv eingeschränkt. Ein Wert von 100 Prozent ist jedoch nur theoretisch zu erreichen, und der in der Realität vorliegende EUSAMA-Wert liegt bei neuwertigen Dämpfern je nach Fahrzeugtyp zwischen 60 und 80 Prozent.
Grundsätzlich kann mit dem EUSAMA-Messprinzip eine globale Aussage über die Fahrsicherheit eines Fahrzeuges gemacht werden. Dazu zählt der technische Zustand der Komponenten Radaufhängung, Radlager, Reifen und Stossdämpfer. Veränderungen am Fahrwerk wie beispielsweise Sportfahrwerke oder die Umstellung auf Breitreifen können die Ergebnisse stark beeinflussen.
Geräusch-Suche
Moderne Fahrwerktester können auch als Geräusch-Suchgerät benutzt werden, um Fahrsituationen zu simulieren, bei welchen der Kunde Fahrzeuggeräusche reklamiert. Dazu wird das Fahrzeug mit einer Achse auf den Rüttelplatten positioniert, welche zu rütteln beginnen. Dabei wird ein gewisses Frequenzspektrum abgedeckt, und die Frequenz lässt sich vom Mechaniker in kleinen Schritten manuell verändern. Ist beispielsweise eine Fahrzeugkomponente nur lose befestigt, wird beim Erreichen ihrer Resonanzfrequenz die Geräuschentwicklung höher, und das entsprechende Teil lässt sich leicht finden.
Spurplatten
Die Spurplatte zur Radlaufprüfung besteht aus einer seitlich verschiebbaren Platte. Fährt der Prüfer mit dem Rad eines Fahrzeuges darüber, kann sich die Platte unter dem Einfluss der Kräfte, welche vom rollenden Rad ausgeübt werden, seitlich verschieben. Diese Seitenkräfte entstehen, weil ein Rad teilweise seitlich über die Fahrbahn gezogen wird, wenn der Spurwert nicht korrekt eingestellt ist.
Beim Überfahren der Spurplatte wird die Abweichung der Achsgeometrie zum Sollwert über Sensorikkomponenten aufgezeichnet. Eine integrierte Mikroprozessorsteuerung wertet die Messergebnisse aus, so dass dem Benutzer «grobe» Informationen über die Achsgeometrie des gesamten Fahrzeuges zur Verfügung stehen. Um detailliertere Ergebnisse sämtlicher Radgeometrie-Daten zu erhalten, ist das Fahrzeug mit einem entsprechenden Lenkgeometrie-Vermessungsgerät zu testen.