Genauere Crash-Simulation entwickelt
Posted by: Unknown author
Ford-Ingenieure haben eine neue virtuelle Testmethode entwickelt, um das Verhalten von faserverstärkten Kunststoff-Komponenten in Crash-Szenarien genauer vorherzusagen. Im Zuge dessen sollen solche leichten und damit CO2-arme Fahrzeuge schneller entwickelt werden können.
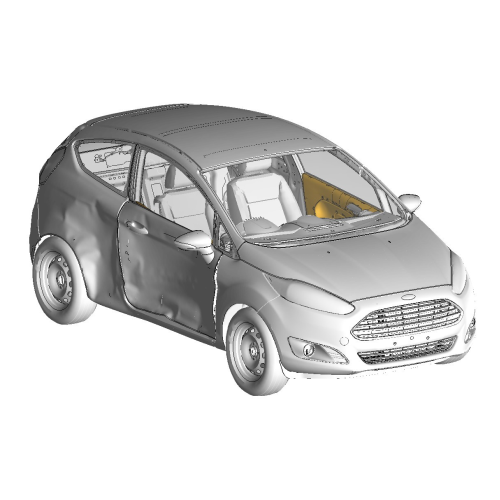
Leichte, faserverstärkten Kunststoff-Komponenten sollen schneller in Fahrzeugen zum Einsatz kommen. Denn leichtere Autos sparen mehr Treibstoff und CO2. Dabei dürfen sie aber keine Einbussen bei der Fahrzeugsicherheit nach sich ziehen. Die neue Prüftechnik soll nun das Verhalten solcher Komponenten in Crash-Situationen genauer vorhersagen und wurde von Ingenieuren des europäischen Ford-Forschungszentrums in Aachen gemeinsam mit der MATFEM-Partnerschaft Dr. Gese & Oberhofer, München, sowie der SIGMA Engineering GmbH, Aachen, entwickelt.
Die neue Testmethode kombiniert zwei bestehende Simulationstechnologien: die 3D-Simulationen des Spritzgussverfahrens, die zeigen, wie Prozessänderungen die Struktur der Kunststoff-Komponenten beeinflussen, und die simulierte Stresseinwirkung (Crash) auf die faserverstärkten Kunststoff-Komponenten, um die Material-Verformungen und -Spannungen voraussagen zu können. So können bereits in einem frühen Stadium der Komponenten-Entwicklung Voraussagen zur Widerstandsfähigkeit der Glasfasern gemacht werden und es werden weniger real hergestellte Test-Prototypen benötigt.
Ford verwendet gewichtsoptimierte, faserverstärkte Kunststoffe bisher beispielsweise in Instrumententafeln, in Türverkleidungen und im Bereich der Karosserie-Komponenten wie den Stossfängersystemen, um den Insassen- und Fussgängerschutz zu verbessern. Das betrifft die Baureihen Fiesta, B-MAX, C-MAX, Focus, EcoSport, Mondeo, Galaxy und Transit. In Zukunft könnten diese Materialien auch für Fahrzeugsitze oder andere Bauteile verwendet werden. (pd/md)