Das Auto wird (fast) neu erfunden
Posted by: Unknown author
BMW steckt mitten in der Entwicklungsphase eines neuen Stadtautos. Das Projekt nennt sich Megacity Vehicle (MCV) und startet 2013 mit Elektroantrieb unter einem Subnamen von BMW. Kernstück ist eine leichte Karosserie mit kohlefaserverstärktem Kunststoff (CFK).
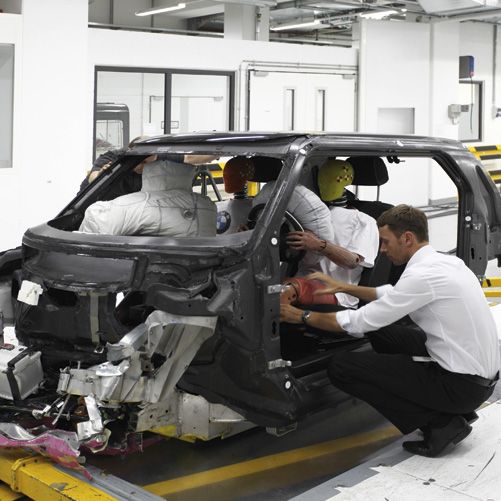
Langer Weg zur Serie: Eine Kohlefaser-Karosserie sowie ein Rahmen und Aufhängungsteile in Aluminium geben erste Anhaltspunkte, wie der Megacity (hier nach einem Crash-Test) aussehen könnte.
VON HANSPETER RENNHARD
BMW hält bei der Elektrifizierung nichts davon, einem bisherigen Modell einfach einen Elektroantrieb zu verpassen. Die Zukunft sieht das bayerische Unternehmen in einem neuen Gesamtkonzept. Problem Nummer eins sind und bleiben die Batterien, denn wenn man eine angestrebte Reichweite von 150 Kilometern erreichen will, wird die Batterie gemäss heutiger Lithium-Ionen-Technik gut 300 kg wiegen.
Aus der Formel 1
Dieses Mehrgewicht will BMW nicht einfach auf eine bisherige Karosserie aufaddieren. Deshalb entwickelt der bayerische Hersteller an einem völlig neuen Gesamtkonzept. Glaubt man ersten bei der Forschung in München am Innovation Day gesehenen Studien, dann basiert die Neuheit auf einem als Drive-Modul bezeichneten Aluminiumträger (Rahmen mit Batterie und Achsen), auf welchen dann eine CFK-Karosserie (Life-Modul) sitzt – vorerst als viertürige Limousine mit Platz für vier Personen sowie Kofferraum. Dieses Konzept, das die Abkehr von der traditionellen selbsttragenden Karosserie sein könnte, wäre aber auch die Basis für andere Karosserievarianten. In die Karten schauen liess sich auch BMW-Designchef Adrian van Hooydonk noch nicht und er sagte: «Der Designprozess für dieses Auto ist noch nicht abgeschlossen und wir haben auch noch keine finale Design-Bestätigung vom Vorstand.» Insgesamt beschäftigen sich im Moment 15 Designer an der Optik des Megacity. Einem BMW-Vorgänger dürfte das MCV nicht gleichen, und es wird möglicherweise ohne die typische BMW-Niere des Weges kommen.
BMW will dank CFK bei der Karosserie rund 100 kg einsparen, wie das an diesem Workshop in München auch CFK-Fachmann Jochen Toepker bestätigte. Produziert werden die Karbonfasern in den USA. In Wackersdorf (D) werden diese zu Matten gewoben und im BMW-Werk Landshut weiterverarbeitet. Die Produktion des MCV soll in Leipzig erfolgen. Ganz interessant, dass 40 bis 50 Leute in diese Entwicklung eingebunden sind, welche sich bis zum Ausstieg von BMW aus der Rennsport-Königsklasse noch der Formel 1 gewidmet hatten. Nicht zufällig, denn auch das F1-Monocoque besteht bekanntlich aus CFK und hat sich – die TV-Bilder zeigen dies jeweils – als sehr stabil erwiesen.
Premium-Gedanke bleibt
Von einem Billig-Kleinwagen will BMW natürlich nichts wissen, unter vier Meter wird es wohl nicht gehen und das Label Premium soll auch diesem Auto auf den Weg mit gegeben werden. Auch sicherheitsmässig wird es keine Kompromisse geben, die ersten Crash-Tests mit Rohkarossen geben erste Anhaltspunkte zum Crash-Verhalten. Bezüglich Leistung liegt die Messlatte bei etwa 125 kW, das Drehmoment bei 250 Nm. Vorerst zielt das MCV auf den reinen Elektroantrieb. Doch man denkt in München auch an weitere Möglichkeiten wie Hybrid-Antrieb oder eine Variante mit Range Extender, womit den Reichweiten kaum Grenzen gesetzt wären. Gemäss den BMW-Ingenieuren ist es jedoch sehr wichtig, dass die Weiterentwicklung der Batterietechnik vorangetrieben wird, denn soll der automobile Elektroantrieb schnell an Fahrt gewinnen, so sind in erster Linie in diesem Bereich weitere Entwicklungssprünge nötig.
CFK: WERKSTOFF DER ZUKUNFT
Kohlenstofffaserverstärkter Kunststoff (CFK) besitzt zahlreiche positive Eigenschaften in einzigartiger Kombination. Dabei sind die Fasern in eine Kunststoffmatrix (Harz) eingebettet. Damit ist CFK stabil und rund 50 Prozent leichter als Stahl. Ausserdem ist dieser Werkstoff, der auch bei Flugzeugen eingesetzt wird, resistent gegen Korrosion, Säuren sowie organische Lösungsmittel und somit langlebiger als Metall. Zudem bleibt CFK unter allen klimatischen Bedingungen stabil und verformt sich auch unter hohen Temperaturschwankungen kaum.
BMW verwendet CFK für verschiedene Einzelteile schon seit 2003. Inzwischen wurde der Fertigungsprozess für CFK-Bauteile im Werk Landshut optimiert und automatisiert, so dass nun auch die wirtschaftliche Grossserienfertigung von Karosseriekomponenten möglich ist. BMW denkt natürlich auch über den Produktzyklus hinaus und entwickelt parallel dazu ein Recyclingkonzept. (hpr)