Vom Ankurbeln zum Einschalten
Posted by: Unknown author
Bis 1912 mussten weltweit alle Automotoren angekurbelt werden. Cadillac setzte erstmals den elektrischen Starter ein. Bis in die 1960er-Jahre fand man in den Stossstangen der Autos jedoch noch Bohrungen für die Kurbeln, obschon diese nur noch für Notfälle gedacht waren. In der heutigen Zeit werden die Anlassvorgänge in Start- Stopp-Systemen automatisiert und man hört auch von anlasserlosen Direktstartsystemen.
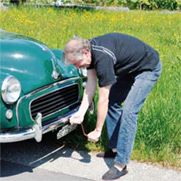
Bis in die 60er-Jahre waren trotz elektrischen Startern viele Fahrzeuge noch mit einer (Not-) Kurbel ausgerüstet.
Während elektrische Geräte seit jeher eingeschaltet werden konnten, mussten die Verbrennungsmotoren immer hochgefahren werden. Der Grund liegt darin, dass Elektromotoren ihre maximalen Drehmomente im Stillstand abgeben, während Verbrennungsmotoren eine Drehzahl von gegen 700/min benötigen, um nur das Drehmoment aufzubringen, welches zum Selbstlauf benötigt wird. Geschieht das Hochfahren durch eine elektrische Maschine über ein (geradeverzahntes) Stirnradgetriebe, dauert der Vorgang, abhängig vom elektrischen Drehmoment einige Sekunden mit den entsprechenden, zahnradbedingten Geräuschemissionen.
Startvorgang Der konventionelle Startvorgang läuft nach dem Diagramm, Bild 2 ab. Dabei stellt die rote Kurve (2) das elektromotorische Drehmoment dar. Dieses ist bei einem Hauptschlussmotor, bei welchem die Feld- und Ankerwicklungen in Serie liegen um so grösser, je kleiner die Drehzahl ist. Die blaue Kurve 1 stellt dagegen das Drehmoment des Verbrennungsmotors dar. Dieser kann kein Drehmoment erzeugen, wenn er keine Drehzahl aufweist, da er kein Gasgemisch ansaugen und verbrennen kann. Die schwarze Kurve (3) addiert die Momentanwerte der Kurven 1 und 2. Sie stellt das gesamte Drehmoment dar, welches der Verbrennungsmotor zusammen mit dem Startermotor abgeben könnte, wenn der Verbrennungsmotor bereits regelmässig arbeiten würde. Das «Anstottern » des Verbrennungsmotors stellt aber die Kurve 4 (grün) dar. Gelingt eine erste Verbrennung (Punkt A), steigt das Drehmoment schlagartig an, können jedoch darauf wieder Verbrennungstakte nicht genutzt werden, fällt das Drehmoment wieder auf die rote Anlasserkurve zurück und der Motor wird nur elektrisch weiterbewegt. Im Punkt B setzen die regelmässigen Verbrennungen des Motors ein und in Punkt C wird der Startermotor ausgeschaltet. Konventioneller Starter Die Zeit und die Geräusche der Schubschraubtriebstarter sind uns seit Jahrzehnten bekannt. Die gängigen Startermotoren sind elektrische Gleichstrommotoren mit Kommutatoren, deren Feld und Anker in Serie geschaltet sind oder die ein permanent erregtes Feld aufweisen. Drehmomente permanent erregter Motoren werden zusätzlich über ein Planeten- oder ein Stirnradgetriebe übersetzt; dabei erreichen sie die erforderlichen Startdrehmomente, und ihre hohen Drehzahlen werden herabgesetzt. Stopp-Start-Funktionen Vor gut 10 Jahren sind die ersten Fahrzeuge mit sogenannten Stopp-Start-Funktionen auf den Markt gekommen. Im verbrauchsrelevanten NEFZ-Zyklus bringen diese Systeme bis 12% Verbrauchseinsparungen. Im Aufbau unterscheiden sich die ersten Systeme kaum von den herkömmlichen Starteranlagen mit Anlassermotoren. Die Kohlebürsten wurden vielleicht verlängert, um der grösseren Anzahl von Startvorgängen gerecht zu werden. Auch die Einspursysteme wurden verstärkt und das Ritzel verbreitert. Steuerungsmässig war der grösste Teil der Elektronik im Getriebesteuergerät untergebracht. So sind Stopp-Start-Systeme nur in Funktion, wenn gewisse Randbedingungen eingehalten werden: Der Bremsdruck muss während einer bestimmten Zeit einen gewissen Wert aufweisen, die ABS-Drehzahlfühler müssen den Fahrzeugstillstand melden, die Kühlflüssigkeitstemperatur muss eine gewisse Temperatur erreicht haben und die Generatorbelastung darf einen bestimmten Wert nicht überschreiten. Wird die Bremse gelöst, gibt das Getriebesteuergerät den Startvorgang wieder frei, indem das Relais (Bild 4) an Masse geschaltet wird. Damit gelangt der Strom in das Anlassersteuergerät, welches den Startvorgang des Motors steuert. Startvorgang In der ersten Phase (Bild 5) werden die Einzugs- und die Haltewicklung des Einrückrelais auf dem Startermotor bestromt. Nachdem der Leerweg des Einrückhebels überwunden ist, wird in Phase 2 der Strom etwas vermindert um das Ritzel sanft auf den Zahnkranz auftreffen zu lassen. In der dritten Phase steigt der Strom wieder an und das Ritzel spurt ein. Erst jetzt wird die Kontaktbrücke geschlossen und der Hauptstrom fliesst zum Startermotor, welcher zu drehen beginnt. In dieser Phase wird die Einzugswicklung stromlos und nur die Haltewicklung hält das Ritzel in der Position. Wird dem Getriebesteuergerät der Motorlauf gemeldet, kann der Startvorgang abgebrochen werden. Riemen-Starter-Generatoren Um die Startgeräusche zu vermindern, um Gewicht einzusparen und um kleine Hybrideigenschaften zu übernehmen, sind heute riemengetriebene Starter- Generatoren auf dem Markt. Dabei kann der Alternator nicht nur die Aufgabe des Generators übernehmen, sondern er kann auch als Motor betrieben werden und so den Verbrennungsmotor über den Mehrrippenriemen starten. Mechanisch ist dabei vor allem ein Augenmerk auf den Riemen und den Riemenspanner zu legen. Der aufwändige und ungewöhnliche Riemenspanner ist im Bild 6 deutlich zu erkennen. Der Spanner greift einerseits vor und andererseits nach der E-Maschine in den Riemen. Treibt die elektrische Maschine die Kurbelwelle an, darf der Riemenspanner nicht auf der gleichen Seite wirken, wie wenn der Riemen von der Kurbelwelle angetrieben wird. Citroën baut im Modell C3 für den Starter-Generator den Riemenspanner nur auf der einen Seite der E-Maschine. Wird sie jedoch motorisch betrieben, kann der Spanner hydraulisch blockiert werden (Bild 7). Elektrische Lösungen Auch wenn das Gehäuse jenem eines Alternators gleicht, hat sich der innere Aufbau etwas verändert. Nach wie vor gibt es den drehenden Klauenpolläufer und darum herum die drei Ständerwicklungen in Stern- oder Dreieckschaltung. Die ganze Gleichrichtung wird jedoch aus dem Generator in ein spezielles Steuergerät verbannt. Das ist nötig, da die Gleichrichterdioden ein Betreiben eines Alternators als Motor verhindern würden. Um genau zu wissen, wie der Rotor (Klauenpolläufer) in der Maschine steht und um die genaue Drehzahl zu kennen, sind drei Hallsensoren integriert, welche über drei Informationsleitungen, eine Masse und eine Versorgungsleitung das Steuergerät mit den Daten versorgen. Steuergerät Dem Steuergerät fällt eine zentrale Rolle zu: es überprüft, ob alle Bedingungen für ein automatisches Abschalten des Verbrennungsmotors gegeben sind und merkt, in welchem Moment dieser wieder gestartet werden muss. Als zweite wesentliche Aufgabe muss es während dem Starten aus der anliegenden Gleichspannung der Batterie in einem Wechselrichter dreiphasigen Wechselstrom (Drehstrom) erzeugen und diesen phasengerecht an die E-Maschine übermitteln. Die Synchronisation wird aufgrund der Hallgeberinformationen erfolgen. Daneben muss während dem motorischen Betrieb der Klauenpolläufer zur Erzeugung eines magnetischen Reaktionsfeldes ebenfalls bestromt werden. Ein Elektromotor funktioniert nur, wenn sich zwei Magnetfelder anziehen oder abstossen. Als dritte Aufgabe wird der Drehstrom, welcher der Starter-Generator während der Fahrt liefert, nicht mittels Dioden, sondern mittels Transistoren gleichgerichtet. Damit auch wieder bekannt ist, in welchen Momenten welche Transistoren durchgeschaltet werden müssen, sind die Hallgeber als Drehzahl- bzw. Positionssensoren unverzichtbar. Zusätzliche Aufgaben Das Starten der Verbrennungsmotoren durch die leistungsfähigen Starter-Generatoren wird heute meistens so gelöst, dass der Verbrennungsmotor fast auf die Leerlaufdrehzahl hochgeschleppt wird. Während dieser kurzen Anschleppphase synchronisieren sich die Einspritzung und die Zündung, damit beim Erreichen der vorgegebenen Drehzahl die Einspritzung aktiviert und vor dem Arbeitstakt auch der Zündfunken ausgelöst werden kann. Bei diesem Startvorgang gibt es keine Verbrennungsaussetzer mehr und der Verbrennungsmotor läuft nach 0.5 – 1 Sekunde mit Leerlaufdrehzahl. Starter-Generatoren können zusätzlich auch Bremsenergie zurückgewinnen. Geht der Fahrer vom Gas, wird die Elektromaschine voll erregt und bremst so das Fahrzeug ab. Die gesamte Energie wird zur Ladung der Batterie eingesetzt. Der Starter-Generator kann auch – wie vor 10 Jahren propagiert, als Kurbelwellen-Starter-Generator zwischen das Schwungrad und den Getriebeeingang gelegt werden. Als Kurbelwellen-Starter-Generator war das System nicht tauglich, heute kennt man aufbaumässig gleiche Systeme und nennt diese Mildhybride. Auch Mildhybride übernehmen die Funktion des Stopp-Startautomaten und können, je nach Betriebsspannung auch Bremsenergie zurückgewinnen oder in gewissen Kennfeldbereichen boosten. Direktstart Mazda stellte am diesjährigen Automobilsalon in Genf das erste Auto mit i-Stop (idle-stop-system) vor. Der Mazda 3 mit dem 2.0-l-Motor und Benzindirekteinspritzung ist weltweit das erste Auto, welches den Startvorgang mit Verbrennungsenergie unterstützt. Um diese Technologie umzusetzen, braucht es sicher einen Motor mit Benzindirekteinspritzung und eine günstige Lageposition des Kurbeltriebes beim Abstellen. Dazu kann der Kurbelwellensensor, welcher auf der Basis von 3 Hallgebern aufgebaut ist, die Position und die Bewegungsrichtung der Kurbelwelle feststellen. Diese Position sollte so sein, dass ein Zylinder kurz nach dem Zünd-OT zum Stehen kommt. So könnte beim Starten eine kleine Menge Benzin eingespritzt und unmittelbar gezündet werden. Damit würde der Druckanstieg den Kolben nach unten bewegen und ein weiterer Zylinder könnte bald darauf bereits effizienter arbeiten. Motorstillstand Der Motor stellt im Stopp-Start- System nur ab, wenn er eine bestimmte Temperatur erreicht hat, die Defroster-Anlage und die Scheibenheizungen nicht in Betrieb sind, das Getriebe sich in der neutralen Position befindet und die Kupplung getreten ist. Dazu muss selbstverständlich die Batterie auf einem guten Ladeniveau sein. Zur Positionsbeeinflussung des Kurbeltriebes haben sich die Mazda-Ingenieure einiges einfallen lassen, um keinen Starter- Generator einsetzen zu müssen. Dieser würde einen Teil des Sparpotenzials des Systems wieder aufbrauchen. Damit der Motor in der richtigen Position stillsteht, kann der Erregerstrom des Alternators nach dem Ausschalten der Zündung noch bis zu einer Drehzahl von 500/min geschalten werden. Damit kann der Motorstillstand beschleunigt werden. Gleichzeitig und bis zum absoluten Stillstand können durch die Ansteuerung der Drosselklappe die Pumpverluste beeinflusst werden. Damit ist der Erfolg garantiert: mit ca. 0,35 Sekunden «Motoreinschaltzeit » schafft der Mazda- Motor den Start ungefähr doppelt so schnell wie ein konventionelles Startsystem.